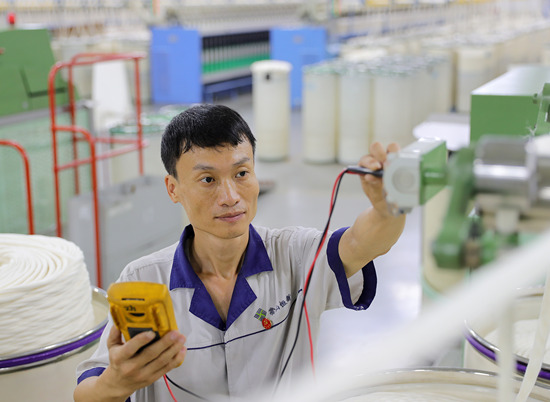
张辉在进行电气设备检测
电气设备是否出现故障、空调设备能否正常运行、车间温湿度是否符合标准……每天早上八点上班后,换上工装的张辉总是习惯性地去车间转一转,检查各种电气设备的工作情况,以保障生产的正常进行。
张辉,是石家庄常山恒新纺织有限公司动力车间主任,也是公司电气维修方面的“技术大拿”。说到这,张辉谦虚地说,“虽然我在电气维修方面取得了一些成绩,但还需要不断学习,不断创新,为企业提供更好的技术服务。”
说起“为什么要到纺织厂工作”,张辉满脸自豪地说:“其实我母亲就是纺织厂工人,小时候带我到厂子里玩,当时就被那么多的纺织机器所震撼,很羡慕在这里工作的人。”1994年,张辉从石家庄纺织技校毕业后,被分配到当时的石家庄国棉五厂从事电气外线维修工作,也算是得偿所愿。
“那会除了体力好、肯学外,对电气知识运用其实是一知半解。”2005年,张辉调到恒新纺织电气车间当电工,第一次独立上岗,在根本看不懂进口设备电路图纸的情况下,糊里糊涂地把线路给维修了,结果造成设备损坏,无法挽救。
从那以后,张辉就暗下决心,一定要把业务水平提上来!工作中,他不断学习,通过社会考试分别取得了维修电工技师和高级技师职业资格;每天上班时,兜里都装着一个小本,遇到的问题全部记上,走到哪里记到哪里,方便他解决问题。
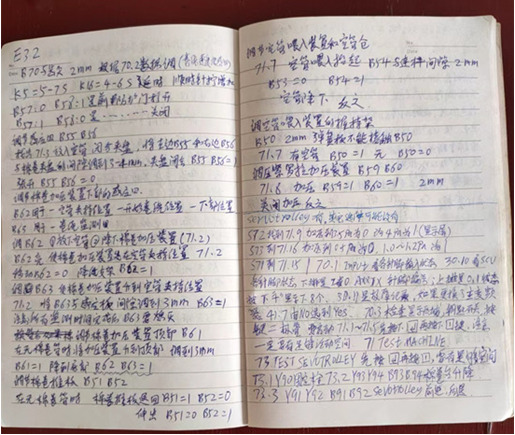
张辉展示以前的问题记录本
“我这个人比较轴,因为热爱这个工作,所以就想做到最好!”张辉说,恒新纺织建厂时,购买了大批“洋设备”,大多数人看不懂进口设备的说明书。为此,张辉找到被搁置多年的英语课本开始重新学习,不会的单词查字典,看到报纸上有英语小文就尝试翻译,利用节假日跑到图书馆去查找翻看《英汉技术科学词典》等专业词典,在他的努力下大部分设备的说明书他都能读懂。
随着知识储备的不断增加,张辉的电气维修技能水平也在不断提升。有一次,德国特吕茨勒清花机在张辉上白班的时候“罢工”了,经检查是一个机台上的直流喂棉电机坏了。这个小电机精密度非常高,按惯例需等进口配件,但一般需要4至7周才能到货,这会影响到生产。怎么办?
“把这个‘洋家伙’的替代品研究出来!”张辉说,进口机器出现故障也不是一、两次了,他们早就开始考虑解决这个问题。趁着这次机会,张辉边琢磨边试验,经过反反复复地比对各种电机参数,最后选了一个交流减速电机,并千辛万苦地给它配上了一个变频器。赶回厂里一试验,机器正常转动了起来,“当时现场的干部职工都高兴地鼓起了掌。”
进口一个德国的原装电机要3万多元,张辉总共才花了两千多元,将“中国造”成功地安装在了以精密而闻名的德国机器设备上,张辉感到非常自豪。
前几年,企业细纱机的用电单耗,吨纱用电量两、三千度,用电量居高不下,问题主要集中在纺纱设备上的吹吸风电机。如何让它能根据实际情况进行吹吸风,减少不必要的“工作”带来的电能空耗呢?张辉仔细琢磨后,认为可以对机器的控制器进行编程,用程序监控它。为了设计控制器编程,张辉又踏上了自学PLC编程之路。
按照职工建议,吹吸风设备启动后,间歇运行时间为“装置休息15分钟,转5分钟比较好。”于是,张辉通过一遍一遍地对控制器程序进行试验和改进,最终设计出让职工满意的程序,这项技改的第一年就为企业节约电费105万元。
从细纱机设备的PLC程序和文本显示器程序的设计修改到清花设备的电气控制改造,再到梳棉机设备的电气线路更改……企业的纺织生产设备几乎被改造了个遍,张辉仿佛“开了挂”,一项一项的技改和创新让企业插上了环保节能的“翅膀”。
“目前,我和我的创新工作室骨干成员正在进行精梳滤尘机组主电机加装变频器节电的技改,这项技改成功后,电耗将由原来的20度/小时降低到12度/小时,每小时节电8度。”张辉说。
在恒新纺织的十几年中,张辉提出并实施技术改造203项,通过优化生产工艺流程,优化纺织设备PLC程序,设计改进生产设备电气控制线路,对进口设备进行新型控制系统国产化替代改造,有效降低设备故障率,提高设备自动化程度,有效降低设备故障率,累计节约电气成本1000多万元。
这期间,他付出的艰辛和不易常人无法想象——
24小时服务,凌晨打车赶到车间排除故障,连坐班车上下班都要思考如何解决技术难题……张辉把工作当成了自己最爱的事业,执着追求,刻苦钻研,从不言弃,勇攀高峰。用他的话说:“纺织工人很辛苦,进到车间就要承受30度左右的温度和巨大的噪音,如果我做不好服务,我连自己都交代不了!”